Industry
Sulfur Scrubbers in Industrial Applications with a Focus on Wet Scrubber Technology
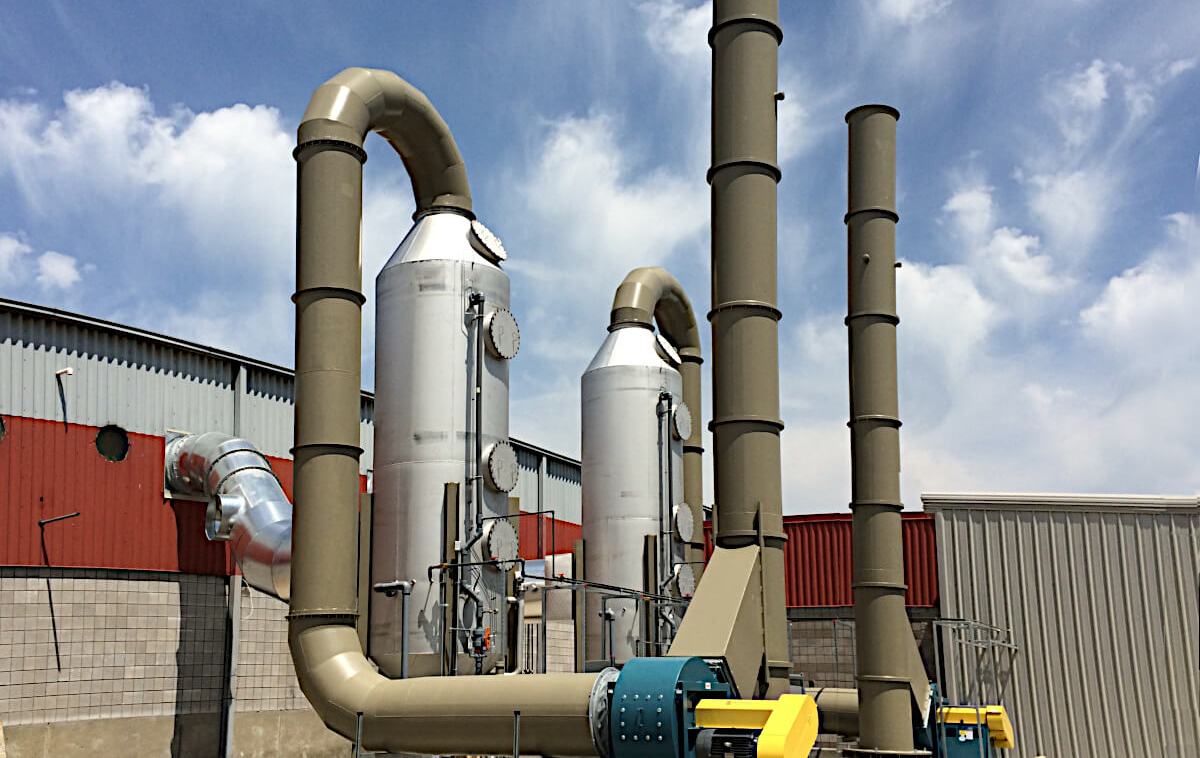
In the industrial and manufacturing sectors, managing sulfur emissions has become increasingly critical due to stringent environmental regulations and the need for sustainable practices. Sulfur scrubbers, specifically wet scrubbers, play a pivotal role in controlling sulfur dioxide (SO₂) emissions. This article explores the importance of sulfur scrubbers, with a focus on wet scrubbers, and provides expert insights into their application in various industries.
Understanding Sulfur Scrubbers
Sulfur scrubbers are devices designed to remove sulfur compounds from exhaust gases generated by industrial processes. These systems are essential in industries such as power generation, oil refining, chemical manufacturing, and metal processing, where sulfur-containing fuels and raw materials are commonly used.
The primary goal of sulfur scrubbers is to prevent the release of sulfur dioxide (SO₂) into the atmosphere. SO₂ is a significant contributor to acid rain, which can have devastating effects on ecosystems, agriculture, and human health. By capturing and neutralizing SO₂ before it is emitted, sulfur scrubbers help industries comply with environmental regulations and minimize their environmental footprint.
The Role of Wet Scrubbers
Among the various types of sulfur scrubbers, wet scrubbers are particularly effective and widely used. Wet scrubbers operate by bringing the exhaust gases into contact with a liquid solution, typically water or a specialized scrubbing liquid, which absorbs and reacts with the sulfur compounds. The resulting reaction produces a byproduct, such as gypsum or sulfuric acid, which can be safely managed or repurposed.
Wet scrubbers are favored in many industries due to their versatility and efficiency. They are capable of removing not only SO₂ but also other pollutants, such as particulate matter and heavy metals, making them a comprehensive solution for emissions control.
Expert Insights on Wet Scrubber Applications
Dr. Michael Turner, an environmental engineer with over 20 years of experience in industrial emissions control, emphasizes the importance of wet scrubbers in the power generation sector. “Coal-fired power plants, which are a significant source of sulfur dioxide emissions, rely heavily on wet scrubbers to meet stringent environmental standards. The ability of wet scrubbers to handle large volumes of gas and achieve high removal efficiencies makes them indispensable in this industry.”
Jane Williams, a chemical engineer specializing in air pollution control, highlights the adaptability of wet scrubbers. “One of the key advantages of wet scrubbers is their ability to be customized to suit different industrial processes. For example, in the oil refining industry, wet scrubbers can be tailored to handle the specific sulfur compounds present in the exhaust gases, ensuring optimal performance and compliance with emission limits.”
Robert Sanchez, an industrial consultant, points out the economic benefits of wet scrubbers. “While the initial investment in wet scrubber technology can be substantial, the long-term cost savings are significant. By reducing sulfur emissions, companies can avoid hefty fines and potential shutdowns, and in some cases, the byproducts of the scrubbing process can be sold or reused, offsetting operational costs.”
Challenges and Future Trends
Despite their effectiveness, wet scrubbers are not without challenges. The maintenance of wet scrubbers can be demanding, as the liquid medium must be regularly monitored and replenished. Additionally, the disposal of the byproducts, such as sludge or gypsum, requires careful management to avoid secondary environmental impacts.
Looking forward, advancements in wet scrubber technology are expected to address these challenges. Innovations such as improved scrubbing liquids, more efficient designs, and integrated systems that combine wet scrubbing with other emissions control technologies are likely to enhance the performance and sustainability of sulfur scrubbers.
Sulfur scrubbers, particularly wet scrubbers, are vital tools in the effort to reduce industrial sulfur emissions. Their ability to effectively remove SO₂ and other pollutants from exhaust gases makes them essential for industries aiming to comply with environmental regulations and reduce their environmental impact. As technology continues to evolve, wet scrubbers are set to become even more efficient, adaptable, and cost-effective, solidifying their role in the future of industrial emissions control.
Industries that invest in advanced sulfur scrubber technology not only contribute to a cleaner environment but also position themselves as leaders in sustainable manufacturing practices.
Industry
How to Find and Choose the Right Used Printing Equipment for Your Business
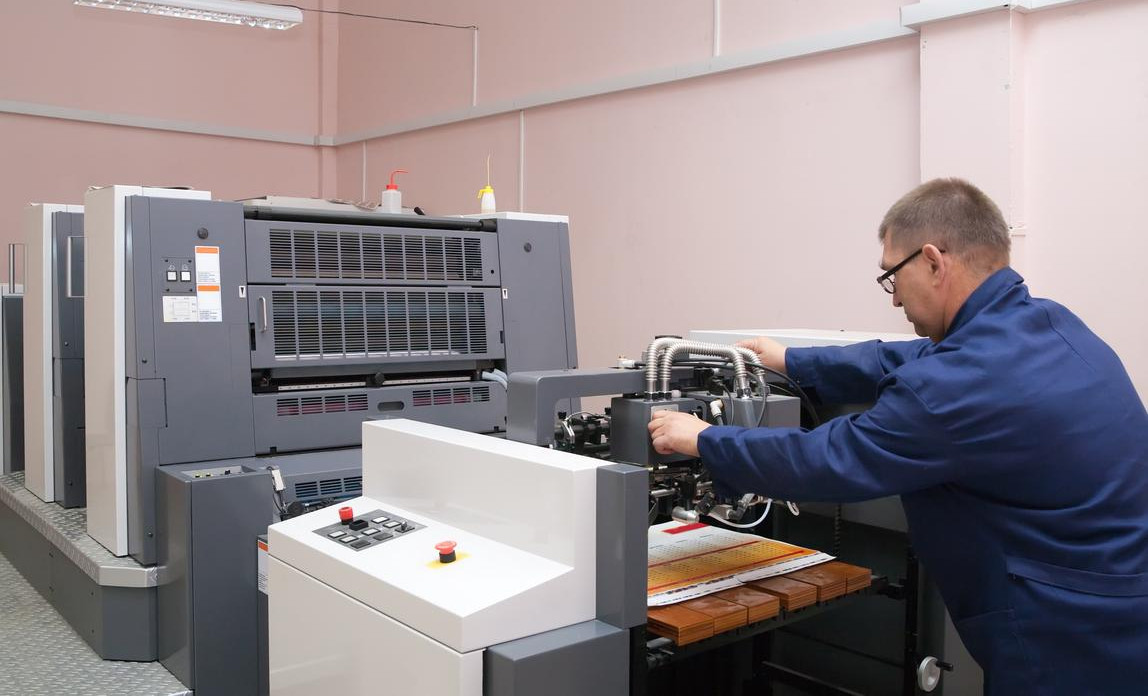
Investing in the right printing equipment is crucial for any business in the printing industry. However, purchasing brand-new machines can be costly, especially for small or growing businesses. Buying used printing equipment offers an affordable alternative that can still meet your production needs without breaking the bank. However, selecting the right printing equipment requires careful consideration to ensure it delivers the quality, efficiency, and longevity your business requires. Here’s a guide on how to find and choose the right used printing equipment for your business.
Why Consider Used Printing Equipment?
- Cost Savings
One of the primary reasons businesses opt for used printing equipment is the significant cost savings. New machinery can be expensive, especially advanced models with enhanced features. By purchasing used equipment, businesses can often secure high-quality machines at a fraction of the original price. These savings can then be redirected toward other essential investments, such as marketing, staff training, or operational expenses. - Faster ROI
Used printing equipment typically offers a quicker return on investment (ROI). Since the upfront cost is lower, it becomes easier to recoup the investment through regular use. Additionally, most of the depreciation has already occurred with used equipment, meaning the machine’s value won’t drop significantly after purchase. - Access to Established Technology
In many cases, used printing equipment includes tried-and-true technologies that have already proven their reliability. This means you can access high-quality machines that have stood the test of time, as opposed to new models that may still be working out initial bugs or glitches.
Steps to Finding the Right Used Printing Equipment
- Assess Your Business Needs
The first step in choosing the right used printing equipment is to evaluate your current and future production needs. Are you looking for a machine that can handle high-volume printing, or do you need equipment that specializes in specific types of printing, such as large format or digital? Understanding your business requirements will help you focus on the types of machines that can best support your operations. - Set a Budget
Even though you’re opting for used equipment, it’s essential to set a budget to avoid overspending. Consider not only the purchase price but also any additional costs, such as shipping, installation, and potential repairs. By having a clear budget in mind, you can narrow down your options and find a machine that fits both your financial limitations and your production needs. - Research Reliable Brands
Some printing equipment brands are known for their durability and longevity, making them ideal candidates for purchasing second-hand. Brands such as Heidelberg, Canon, Xerox, and Komori have established reputations for producing robust machines that can stand the test of time. Opting for a well-known brand can give you more confidence in the machine’s long-term performance, even if it’s pre-owned. - Check for Availability of Parts and Support
Before committing to a purchase, ensure that the model you’re considering still has parts and support available. Older machines may no longer be supported by the manufacturer, and finding replacement parts could be a challenge. “It’s essential to verify the availability of spare parts and service support for any used printing equipment you’re considering,” says Paul Harrison, a veteran in the printing equipment industry. “Otherwise, you may find yourself with a machine that becomes unusable after a breakdown.” - Research Sellers and Dealers
To ensure you’re buying from a reputable source, it’s important to thoroughly research dealers who specialize in used printing equipment. Look for businesses with a history of positive customer feedback, clear return policies, and equipment warranties. It’s advisable to avoid private sellers unless you have expert knowledge of the machine you’re buying. A professional dealer often inspects and refurbishes the equipment to ensure it is in working order.
Key Considerations When Choosing Used Printing Equipment
- Age and Condition of the Equipment
The age of the machine and its condition are critical factors to consider. Older machines may have more wear and tear, which could lead to frequent breakdowns or diminished performance. Always ask about the machine’s history, including its usage, maintenance records, and whether it has undergone any major repairs. A thorough inspection is necessary to ensure the machine is in good working order before purchase. - Test the Equipment
Whenever possible, test the machine before buying it. This allows you to assess its functionality and ensure it meets your quality standards. If a live test is not possible, request a demonstration video from the seller. “Testing used printing equipment in person gives you a clear idea of its performance and whether it aligns with your production goals,” says Karen Thompson, a printing operations consultant. “You can verify the machine’s output quality and check for any operational issues.” - Verify Production Output and Capabilities
Different machines are designed to handle various types of print jobs, such as offset, digital, or large-format printing. Make sure the used machine you’re considering is capable of handling the volume and types of printing required by your business. Additionally, verify whether the machine can be upgraded or modified if your production needs grow in the future. - Warranty and Return Policy
Purchasing used equipment involves some level of risk, so it’s important to check whether the seller offers any type of warranty or return policy. Even if it’s a limited warranty, having some protection can give you peace of mind that the machine won’t fail right after purchase. Also, clarify the terms of any return policy in case the machine doesn’t perform as expected. - Consider Transport and Installation
Used printing equipment is often large and complex to install. Consider the logistics of transporting the machine to your location and whether installation services are provided by the seller. Some dealers offer delivery and setup as part of their package, while others may charge extra or expect you to handle it independently.
Finding and choosing the right used printing equipment can be a cost-effective way to expand your business’s production capabilities without the high expense of buying new machines. By carefully assessing your business needs, setting a budget, researching reliable brands and sellers, and inspecting equipment thoroughly, you can make an informed decision that will benefit your business for years to come. With the right approach, you can secure a high-quality, durable printing machine that offers excellent value and performance, helping your business thrive in the competitive printing industry.
Industry
Ocado Launches Trial for Refillable Packaging to Reduce Single-Use Plastic
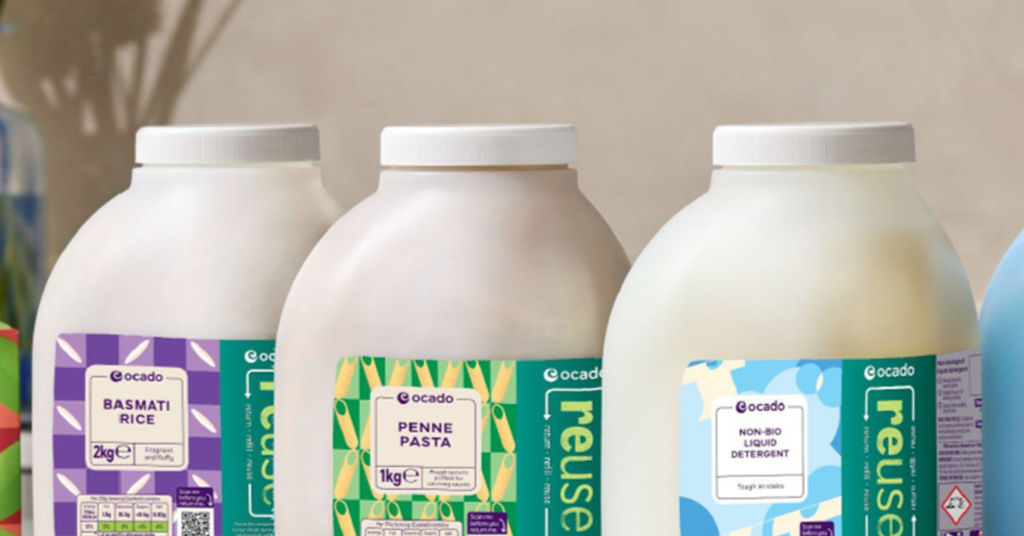
Online grocery retailer Ocado has announced a new initiative aimed at reducing single-use plastic by introducing refillable packaging for everyday items. The trial, set to begin this month, will offer customers products such as rice, pasta, and laundry detergent in reusable containers, marking a significant step in the company’s efforts to promote sustainability.
Under the new “Ocado Reuse” brand, these refillable products will be delivered to customers in specially designed containers. After use, the empty containers will be collected by Ocado drivers during the customer’s next delivery. The containers will then be inspected, cleaned, and refilled for future use, creating a circular system that minimizes waste.
The trial will be rolled out in two phases. The initial phase, starting this month, will include items like 2kg bags of basmati rice and 1kg packets of penne pasta. The second phase, expected to launch in the coming months, will introduce 3-liter containers of fabric conditioner and non-bio liquid detergent. Notably, Ocado will not charge any additional fees for the reusable packaging, and customers will have the option to select both delivery and collection services for these refillable products.
Simon Hinks, Ocado Retail’s product director, emphasized the convenience of this new system for customers, drawing parallels to the company’s existing bag recycling program. “Most people understand the concept and how it works in a physical store, but this trial brings refillable packaging straight to customers’ doors,” Hinks told The Guardian. “Our customers are already used to giving their bags back to our drivers for recycling—so this is a really sensible next step for us to help our customers reduce single-use plastic on products they buy frequently.”
To develop this initiative, Ocado collaborated with The Refill Coalition, a UK-based group dedicated to scaling refilling solutions for supermarkets. The reusable containers, designed and supplied by Berry Global, can each replace up to five single-use plastic containers or packets and are capable of being reused approximately 60 times.
Ocado’s efforts to promote refillable options are in line with consumer demand. A recent poll conducted by the supermarket revealed that one in three UK adults already opts for refillable products for at least one everyday item. Additionally, 75% of those surveyed expressed willingness to embrace more refillable options, provided prices remain stable and product quality is maintained.
In a related development, Ocado has also partnered with Alcampo to open Spain’s first Customer Fulfilment Centre (CFC), a state-of-the-art automated warehouse that utilizes robots, artificial intelligence, and other advanced technologies to streamline the order fulfillment process. This collaboration aims to enhance the quality and efficiency of online grocery services in Spain, further cementing Ocado’s commitment to innovation and customer satisfaction.
-
Business1 year ago
Saudi Arabia’s Model for Sustainable Aviation Practices
-
Business1 year ago
Recent Developments in Small Business Taxes
-
Politics1 year ago
Who was Ebrahim Raisi and his status in Iranian Politics?
-
Business11 months ago
Carrectly: Revolutionizing Car Care in Chicago
-
Business11 months ago
Saudi Arabia: Foreign Direct Investment Rises by 5.6% in Q1
-
Technology1 year ago
Comparing Apple Vision Pro and Meta Quest 3
-
Politics1 year ago
Indonesia and Malaysia Call for Israel’s Compliance with ICJ Ruling on Gaza Offensive
-
Sports10 months ago
Keely Hodgkinson Wins Britain’s First Athletics Gold at Paris Olympics in 800m